Solutions
Products
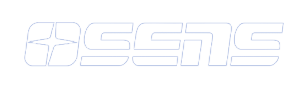
Date:2023-11-30 Categories:Technical CaseHits:463From:osensinc
Definition of damping
Damping (Damping) refers to the gradual decline in the vibration amplitude of any vibration system due to external effects (such as fluid resistance, friction, etc.) and the inherent causes of the system itself, and the quantitative characterization of this characteristic.
In the actual vibration, because friction always exists, the energy initially obtained by the vibration system, in the vibration process due to the resistance of the system continues to do negative work, so that the energy of the system continues to reduce, the intensity of vibration gradually weakened, the amplitude is smaller and smaller, so that finally stop the vibration, such as the system, mechanical energy due to friction and transformed into internal energy gradually reduced. The amplitude decreases with time, which is called damped vibration.
When the damping is strong, the damped oscillator has almost no vibration, and the amplitude gradually decreases to achieve a stable equilibrium, which is called overdamping.
When the damping is weak, the damping oscillator must slowly reduce the amplitude through multiple vibrations and finally return to the equilibrium position, so the time to achieve a stable equilibrium is longer, which is called underdamping.
The other case is that the damped oscillator reaches stable equilibrium with the most stable speed and the shortest time, which is called critical damping.
In layman's terms, it means stopping something from moving. When an object is vibrated by an external force, it will produce a reaction force that attenuates the external force, which is called the damping force (or damping force), and the ratio of it to the force is called the damping coefficient.
Usually the direction of the damping force is always opposite to the direction of the velocity. Therefore, the greater the damping coefficient of the material, the better its damping effect or damping effect. However, it is not the greater the damping the better, the damping to a certain extent between the two objects into a rigid connection, damping is generally used with the spring, damping is too large, will not be able to buffer the effect.
The function and basic method of damping
1. The specific role of damping
Damping helps to reduce the resonance amplitude of the mechanical structure, so as to avoid structural damage caused by the limit of dynamic stress.
Damping helps the mechanical system to quickly return to a stable state after an instantaneous shock.
Damping helps to reduce the sound radiation caused by mechanical vibration and reduce mechanical noise.
It can improve the machining accuracy, measuring accuracy and working accuracy of all kinds of machine tools and instruments.
Damping helps reduce the structure's ability to transmit vibration.
2. Basic methods of damping
System damping: Set special damping shock absorbers in the system, such as damping springs, shock dampers, etc.
Structural damping: an additional material or an additional structure is formed on a vibration structure of the system to increase the damping capacity of the system itself, such methods include joint surface, Coulomb friction damping, pumping damping and composite structure damping.
Material damping: relying on the high damping characteristics of the material itself to achieve the purpose of vibration and noise reduction. It includes viscoelastic material damping, damping alloy damping and composite material damping.
Relevant standards for damping tests
The most commonly used parameter to evaluate the damping properties of damping materials is the composite loss factor, and the cantilever beam bending resonance method is generally used in various industries.
ISO-6721 plastics - Determination of dynamic mechanical properties
ASTM - E756 Standard test method for measuring Vibration reduction properties of materials
Laboratory measurement of combined vibration damping properties of materials on SAE-J1637 support steel rods
GB/ T-16406 Acoustics - Bending resonance test method for damping properties of acoustic materials
GB/ T-18258 Damping material damping performance test method
The instrument of the test system consists of two parts: excitation and detection. An excitation signal is generated by the signal generator, and the exciting force is applied to the sample through the non-contact exciter. The vibration response signal of the sample is detected by the detection sensor. The resonance curve of the sample is measured by keeping the excitation amplitude constant and changing the frequency continuously. According to the measured resonance frequency and half-power bandwidth, the composite loss factor of the composite spline can be calculated, as shown in the figure. If the test process is done in a temperature-controlled chamber, the effect of temperature on the damping characteristics of the material can be determined.
1. According to the different classification methods of excitation and damping
Hammer pulse excitation - frequency domain test damping
Piezoelectric ceramics wideband random excitation-frequency domain test damping
Vibration table sweep excitation - frequency domain test damping
Vibration table fixed frequency resonance excitation - time domain test damping
2. Comparative analysis of results
Repeatability: Vibration table sweep excitation is the best, the human factor is small. Hammering method has poor repeatability.
Accuracy: Vibration table sweep frequency excitation is the best.
Frequency range: Piezoelectric ceramics can be used for high-frequency damping tests, and the vibration table can measure damping up to 2400Hz.
Efficiency: Hammering method is the most convenient and fast, and the hardware cost is low; The hardware cost of piezoelectric ceramic and vibration table test damping is quite large, and the test efficiency is also low. However, vibration table excitation can accurately control the excitation force amplitude and signal type, and it is easy to accurately test and evaluate the damping characteristics of some thin plate structures coated with damping damping materials.